厌氧PP三相分离器 PPuasb三相分离器 PP厌氧三相分离器 PP三相分离器 厌氧三相分离器 三相分离器模块 三相分离器 厌氧PP三相分离器
uasb三相分离器中容易出现的连接质量问题
在作为核心组件,其连接质量直接影响系统的运行效率和稳定性。然而,在实际工程应用中,三相分离器的连接环节常因设计、施工或材料等问题导致故障频发。以下从多个角度分析其常见的连接质量问题及解决方案:
在作为核心组件,其连接质量直接影响系统的运行效率和稳定性。然而,在实际工程应用中,三相分离器的连接环节常因设计、施工或材料等问题导致故障频发。以下从多个角度分析其常见的连接质量问题及解决方案:
一、密封性不足导致的泄漏问题
1. 沼气管道连接泄漏
问题表现:沼气管道的焊接或法兰连接处密封不严,导致甲烷泄漏,不仅降低沼气收集效率,还可能引发安全隐患。
原因分析:焊接工艺不达标(如焊缝存在气泡或裂纹)、密封垫片老化或安装不当、法兰螺栓紧固不均匀等。
解决方案:采用专业热熔焊接技术,确保焊缝无缺陷;选用耐腐蚀的密封材料(如氟橡胶垫片),并定期检查更换;法兰连接需使用扭矩扳手确保螺栓受力均匀。
2. 排泥管或出水管接口渗漏
问题表现:排泥管或出水管线的接口处出现污水渗漏,导致污泥流失或出水水质恶化。
原因分析:接口处未清理干净(如残留污泥或杂质)、胶水粘接不牢固、法兰连接未对齐等。
解决方案:施工前彻底清洁管口并打磨平整,使用高强度厌氧胶或环氧树脂胶粘接;法兰连接需校准对中,避免应力集中导致密封失效。
二、结构设计与安装偏差问题
1. 三相分离器位置偏移
问题表现:分离器未垂直安装或位置偏离反应器中心,导致气液固三相流动紊乱,分离效率下降。
原因分析:安装时未使用水平仪校准,或支架固定不稳导致设备移位。
解决方案:安装前通过激光对中仪确定反应器中心位置,并用不锈钢支架固定分离器;定期检查支架螺栓是否松动。
2. 布水系统与分离器衔接不当
问题表现:布水器与分离器之间的水流分布不均,造成局部流速过快,污泥被过度冲刷至出水口。
原因分析:布水孔设计不合理、连接管道直径不匹配或未设置导流板。
解决方案:***化布水孔布局(如采用均布孔或渐缩孔设计),确保进水均匀;连接管道需与分离器入口直径匹配,并增设导流板以平衡水流。
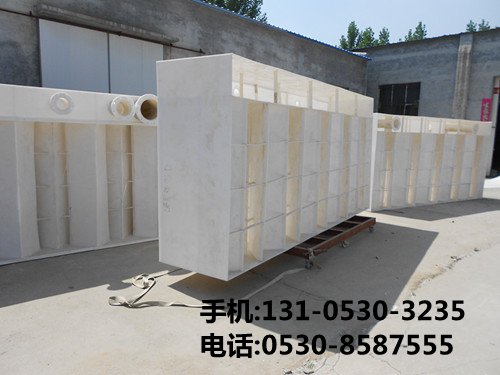
三、材料腐蚀与磨损问题
1. 金属部件腐蚀
问题表现:沼气中的硫化氢(H₂S)腐蚀金属管道或分离器内部构件,导致穿孔或断裂。
原因分析:未选用耐腐蚀材料(如不锈钢316L或玻璃钢),或防腐涂层施工不规范。
解决方案:***先选择耐腐蚀材料(如PVC、PP或钛合金),或对碳钢部件进行环氧沥青涂层处理;定期检测腐蚀情况并更换受损部件。
2. 塑料管材老化开裂
问题表现:排泥管或出水管线因长期接触污水中的化学物质(如酸、碱)而脆化开裂。
原因分析:管材选型不当(如使用普通PVC而非UPVC),或未考虑环境温度变化的影响。
解决方案:选用耐化学腐蚀的UPVC或HDPE管材,并在低温环境下添加防冻保护措施。
四、动态负荷冲击下的连接失效
1. 污泥回流冲击导致接口松动
问题表现:内循环泵开启时,高速污泥流冲击管道接口,造成法兰螺栓松动或胶水脱粘。
原因分析:接口未设置防震装置,或循环流量超过管道承载极限。
解决方案:在接口处加装橡胶减震垫或柔性接头;通过流量计和阀门控制循环流量,避免过载。
2. 热胀冷缩导致焊缝开裂
问题表现:温差变化引起管道材料膨胀或收缩,导致焊接部位撕裂。
原因分析:未预留伸缩节或补偿器,焊缝抗疲劳强度不足。
解决方案:长距离管道每隔35米设置波纹补偿器;焊接时采用分段退焊法以减少应力集中。
五、维护与监测不足的隐患
1. 隐蔽连接点的检查盲区
问题表现:埋地管道或水下接口的腐蚀、渗漏难以及时发现,导致问题恶化。
解决方案:定期使用内窥镜或超声波检测设备检查隐蔽部位;对关键节点安装在线监测传感器(如压力、流速传感器)。
2. 备用连接件缺失
问题表现:突发泄漏时缺乏备用法兰、垫片或管材,延误维修时机。
解决方案:建立连接件备品库,储备常用规格的法兰、垫片、胶水等材料,并定期检查其性能。
总结与建议
UASB三相分离器的连接质量问题涉及材料选择、施工工艺、结构设计、运行管理等多个环节。为提升连接可靠性,建议采取以下综合措施:
1. 设计阶段:通过流体力学模拟***化布水与分离器衔接结构,选用耐腐蚀、高强度的材料。
2. 施工阶段:严格遵循焊接、粘接工艺标准,使用专业工具校准设备位置。
3. 运维阶段:建立定期巡检制度,重点检查隐蔽连接点;配置应急维修工具和备品。
4. 人员培训:加强对焊接、安装人员的技能考核,确保其熟悉厌氧系统的***殊要求。
通过以上措施,可显著降低三相分离器连接故障的发生率,保障UASB系统的长期稳定运行。