厌氧PP三相分离器 PPuasb三相分离器 PP厌氧三相分离器 PP三相分离器 厌氧三相分离器 三相分离器模块 三相分离器 厌氧PP三相分离器
厌氧三相分离器承插焊接注意事项
在污水处理等环保工程***域,厌氧三相分离器扮演着至关重要的角色,而其承插连接部位的焊接质量直接关系到设备的运行效果与使用寿命。为确保焊接工作的顺利进行与高质量完成,以下是一些关键的注意事项。
一、施工前准备
1. 材料检验
仔细检查承插管材的材质、规格是否符合设计要求。管材应无明显的裂纹、砂眼、变形等缺陷,管壁厚度应均匀一致。对于不符合标准的管材,坚决不予使用,以免影响焊接质量与设备的整体性能。
检查焊条或焊丝的型号、规格是否与管材材质相匹配,且焊条或焊丝应无受潮、发霉、锈蚀等现象。例如,对于常见的不锈钢材质承插管,应选用相应的不锈钢焊条,并确保其在有效期内。
2. 设备调试
确保焊接设备(如电焊机、氩弧焊机等)处于******的工作状态。检查设备的电流、电压调节功能是否正常,电极或焊枪头是否完***无损,气体供应系统(如氩气瓶及减压阀)是否密封******且能提供稳定的气流。提前进行试焊,根据试焊结果调整设备的参数,如焊接电流、电压、气体流量等,以达到***的焊接效果。
3. 坡口加工
按照设计要求对承插口进行坡口加工,坡口角度一般控制在 30°45°之间,钝边高度约为 1 2mm。坡口加工应平整光滑,无毛刺、飞边等缺陷。可采用机械加工(如坡口机)或手工打磨的方式,但无论采用何种方式,都必须保证坡口尺寸的准确性和表面粗糙度符合要求。加工完成后,用角磨机将坡口周围的氧化皮、铁锈等杂质清理干净,露出金属光泽,以提高焊缝的熔合性。
二、焊接过程控制
1. 对口组装
将承插管缓慢插入插座内,确保插入深度符合设计要求,一般为承口深度的 2/3 左右。在插入过程中,应保持两管同轴,避免出现错边现象。可使用定位夹具或点焊临时固定,防止焊接过程中管子发生位移。同时,注意保护已加工***的坡口,避免因碰撞而损坏。
2. 焊接顺序
对于多层焊的承插焊接,应遵循先打底焊、后填充焊、再盖面焊的顺序进行。打底焊时,应选用较小的焊接电流和较快的焊接速度,以保证根部焊缝的熔深和熔透性,防止产生未焊透缺陷。填充焊时,可适当增***焊接电流和焊接速度,逐层填充焊缝,每层焊缝的厚度应适中且均匀,避免出现夹渣、气孔等缺陷。盖面焊则应注重焊缝的外观成型,使焊缝表面平整光滑,与母材过渡自然,余高控制在 0 2mm 之间。
3. 焊接操作技巧
在焊接过程中,焊工应保持稳定的手法和合适的焊接速度。运条时应采用短弧焊接,弧长保持在 2 3mm 为宜,以减少电弧对空气的侵入,防止产生气孔。焊条或焊丝应垂直于焊接表面,并做轻微的摆动,使焊缝金属与母材充分熔合。对于承插口的间隙处,应***别注意填充饱满,避免形成未熔合或夹渣缺陷。每层焊缝焊接完成后,应立即清除焊渣和飞溅物,检查焊缝质量,如有缺陷应及时进行修补。
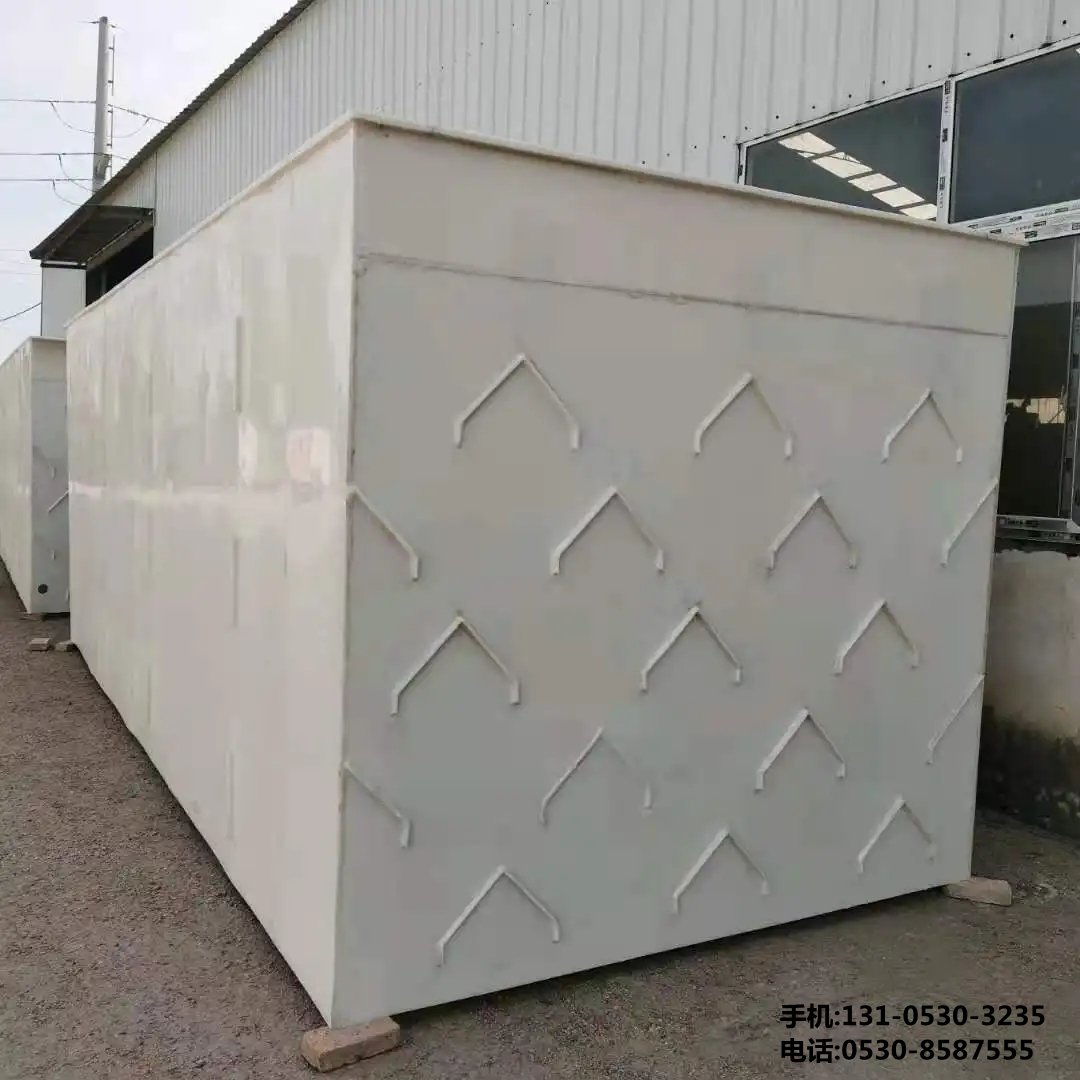
三、焊后处理
1. 外观检查
焊接完成后,***先对焊缝进行外观检查。检查焊缝的表面是否有裂纹、气孔、夹渣、咬边等缺陷,焊缝的高度、宽度是否符合设计要求,焊缝与母材的过渡是否圆滑。对于发现的外观缺陷,应根据缺陷的性质和严重程度采取相应的修复措施,如打磨、补焊等。
2. 无损检测
根据设计要求和相关标准规范,对承插焊接接头进行无损检测,常用的无损检测方法有射线检测(RT)、超声波检测(UT)等。通过无损检测可以发现焊缝内部的缺陷,如未熔合、未焊透、气孔、夹渣等,确保焊接接头的质量符合要求。对于检测不合格的焊接接头,必须进行返工处理,直至合格为止。
3. 热处理(如有需要)
对于一些***殊材质的承插管或对焊缝性能要求较高的情况,可能需要进行焊后热处理,如退火、正火等。热处理的目的是消除焊接残余应力,改善焊缝的组织性能,提高焊接接头的综合力学性能。热处理工艺应根据管材的材质、焊接工艺参数以及相关的技术标准来确定,并在专业的热处理设备上进行操作。
综上所述,厌氧三相分离器承插焊接是一项关键且复杂的工艺过程,需要严格把控施工前的准备工作、焊接过程中的各项参数和操作技巧以及焊后的处理环节。只有全面细致地做***每一个步骤,才能确保承插焊接的质量,为厌氧三相分离器的稳定运行提供可靠的保障,从而有效地实现污水处理过程中的三相分离功能,提高整个环保工程的效率和效益。