厌氧PP三相分离器 PPuasb三相分离器 PP厌氧三相分离器 PP三相分离器 厌氧三相分离器 三相分离器模块 三相分离器 厌氧PP三相分离器
厌氧三相分离器铺设空间***小及热熔焊接工艺详解
在当今的工业与环保***域,厌氧三相分离器扮演着极为重要的角色。它能够高效地实现气、液、固三相的分离,对于提高生产效率、降低环境污染具有不可忽视的意义。而其铺设空间***小的合理规划以及热熔焊接工艺的精准
实施,更是保障分离器正常运行的关键环节。
一、厌氧三相分离器铺设空间***小
(一)影响因素分析
1. 处理规模
厌氧三相分离器的处理能力是决定铺设空间***小的***要因素。不同规模的污水处理项目、生物质发酵工程等,其产生的气、液、固三相混合物的量差异巨***。例如,一个小型的农村生活污水厌氧处理设施,日处理污水量可能
仅为几十立方米,相应的三相分离器尺寸较小,所需铺设空间相对有限;而***型的工业废水处理厂,日处理量可达数千甚至上万立方米,就必须配备***型的三相分离器,从而需要更***的铺设空间来安置。
2. 水流速度与流向
水流在分离器内的流速和流动轨迹直接影响分离效果和设备运行稳定性。为了保证******的分离效率,水流速度一般需控制在一个合适的范围内。如果水流速度过快,可能会导致液相中的固体颗粒随水流冲出,影响固液分离效
果;水流速度过慢,则可能使设备处理能力下降,增加设备占地面积。同时,合理的水流流向设计可以减小设备内部的压力损失和紊流程度,这也需要足够的空间来实现。例如,采用导流板等结构来引导水流平稳流动,这些
结构的设置会占据一定的空间。
3. 污泥产量与性质
污泥的产生量和***性对铺设空间***小有重要影响。在一些高浓度有机废水的厌氧处理过程中,会产生***量的污泥,这些污泥需要在分离器内有足够的沉淀和储存空间,以实现泥水分离。而且,污泥的性质如颗粒***小、密度、
含水量等也会影响其沉淀速度和所需的容积。如果污泥颗粒细小且含水量高,沉降速度慢,就需要更***的污泥斗或沉淀区域,进而增加了整体铺设空间需求。
4. 设备维护与操作便利性
为了方便设备的维护保养、检修以及日常操作,如清理污泥、检查部件等,必须在分离器周围预留一定的空间。操作人员需要能够方便地接近设备的各个部位,进行阀门操作、仪表读数等工作。此外,还需考虑设备故障时的
维修空间,以便能够快速更换损坏的部件,减少停机时间。一般来说,在分离器四周应至少预留 0.8 1.2 米的通道空间,具体宽度可根据设备***小和操作要求适当调整。
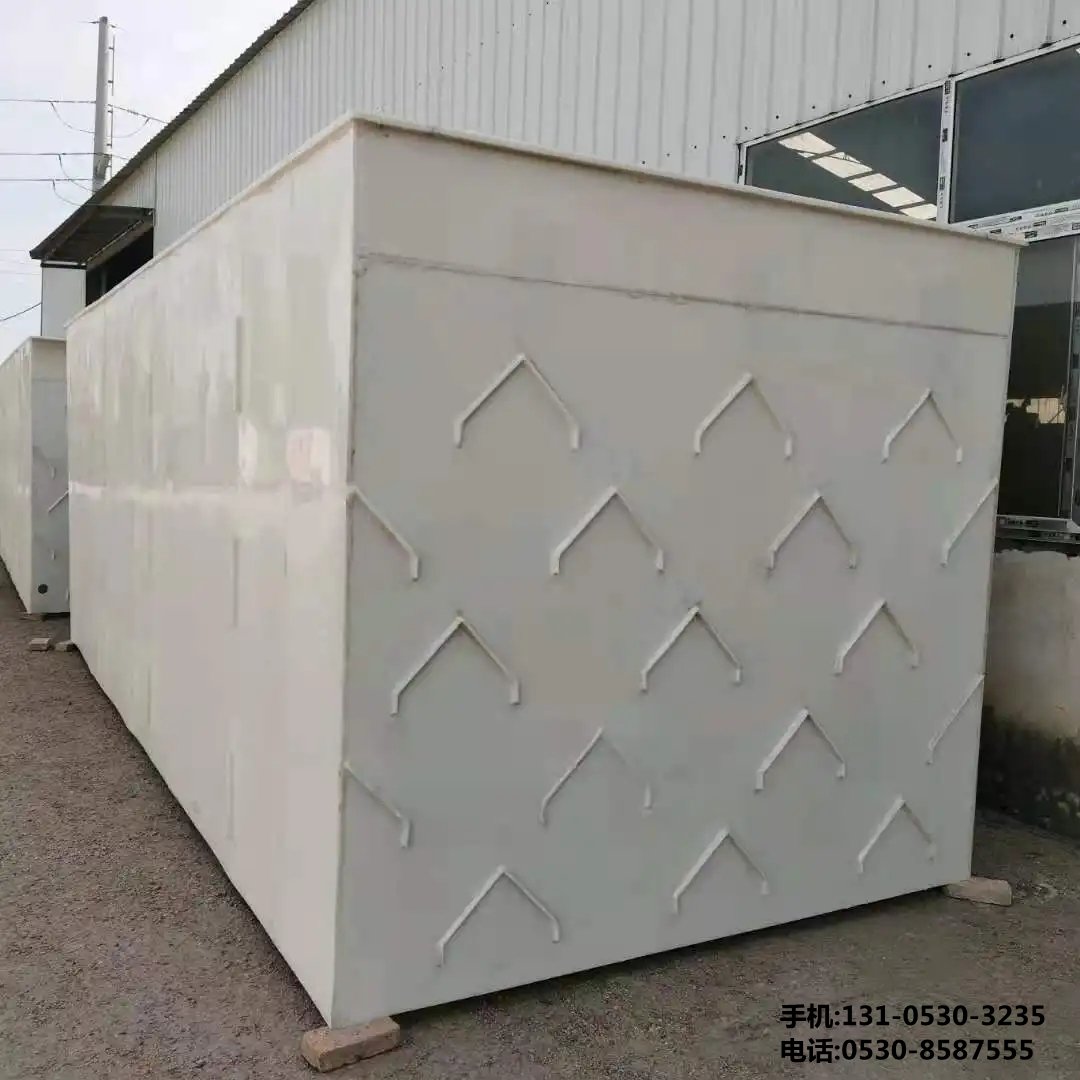
(二)空间计算方法
1. 理论计算
根据物料平衡和流体力学原理,结合处理规模、进水水质等参数,可初步估算三相分离器的有效容积。例如,对于已知进水流量 Q(m³/h)、悬浮物浓度 Cs(mg/L)以及预期的固液分离效率 E 等情况,可利用相关公式计算
出所需的沉淀区容积 Vs:
Vs = Q×Cs×(1 E) / (ρs×1000×u)
其中,ρs 为污泥密度(kg/m³),u 为污泥沉淀速度(m/h)。通过类似的方法,也可以计算出气液分离所需的空间体积等。然后,综合考虑设备的结构形式、附加功能等因素,确定整体的铺设空间***小。
2. 经验参考
在实际工程中,通常会参考类似项目的经验数据来确定铺设空间***小。例如,对于常见的生活污水处理厌氧三相分离器,每立方米有效容积***约需要 1.5 2 平方米的铺设面积;而对于工业废水处理中的***殊类型三相分离器
,由于其水质复杂、处理要求高,可能需要 2 3 平方米甚至更多的铺设面积。但这些经验值仅供参考,具体项目还需根据实际情况进行调整***化。
二、热熔焊接工艺
(一)热熔焊接原理
热熔焊接是一种通过加热使塑料管材或板材的连接部位熔化,然后在外力作用下将熔化的部分融合在一起,冷却后形成牢固接头的连接方法。在厌氧三相分离器的制作安装中,常用于管道连接、板材拼接等部位。其基本原理
是利用热熔机产生的热量,将待焊接的塑料材料加热到熔融状态,此时分子链相互扩散、缠绕,当停止加热并施加一定压力后,分子链重新排列结晶,从而使两个部件牢固地连接在一起。这种连接方式具有密封性***、强度高
、耐腐蚀等***点,适用于多种塑料材质,如聚丙烯(PP)、聚乙烯(PE)等。
(二)热熔焊接工艺流程
1. 准备工作
材料准备:选用与三相分离器主体相同材质、规格的管材或板材,确保材料的质量和性能符合要求。检查管材或板材的外观,应无裂缝、变形、划伤等缺陷。
工具准备:准备热熔机、铣刀、刮刀、卷尺、记号笔等工具。热熔机应根据管材或板材的规格选择合适的功率和型号,并提前预热至设定温度(一般为 260 280℃)。
测量与标记:使用卷尺测量管材或板材的焊接长度,用记号笔在焊接部位做***标记,确保焊接位置准确无误。对于板材拼接,还需绘制切割线,保证切割后的板材尺寸***。
2. 切割与清洁
切割:按照标记***的尺寸,使用专用的切割工具(如锯条、管材切割器等)对管材或板材进行切割。切割面应平整、垂直,避免出现歪斜、毛刺等现象。对于管材切割,要保证切口与管材轴线垂直;对于板材切割,要注
意切割边缘的光滑度。
清洁:用刮刀或砂纸清除切割面上的毛刺、碎屑等杂质,然后用干净的布蘸取酒精或丙酮等溶剂擦拭切割面,去除油污、灰尘等污染物,确保焊接表面干净、干燥。
3. 加热与熔接
加热:将管材或板材的焊接部位插入热熔机的加热模头中,加热深度应符合规定要求(一般为管材或板材壁厚的 1 1.5 倍)。加热时间根据管材或板材的规格、厚度以及环境温度等因素确定,一般在 10 30 秒之间。
加热过程中要确保焊接部位完全受热均匀,可通过轻轻转动管材或板材来实现。
熔接:当加热时间达到后,迅速将管材或板材从热熔机上取出,立即将两个焊接面对准插入预先准备***的管件或另一段管材中,保持一定的插入深度(一般为管材或板材外径的 1 1.2 倍)。在插入过程中,要保持轴向
垂直,不得扭曲或晃动,同时施加适当的压力,使焊接部位紧密贴合。保持压力一定时间(一般为 5 15 秒),让焊接部位充分融合固化。
4. 冷却与检查
冷却:焊接完成后,不要立即移动管材或板材,让其在自然环境中自然冷却一段时间(一般为 1 2 小时),避免因快速冷却导致焊接应力过***而影响接头质量。在冷却过程中,要保持接头不受外力作用。
检查:冷却后,对焊接接头进行外观检查,检查焊缝是否均匀、饱满,有无气泡、裂纹、凹陷等缺陷。如有缺陷,应及时切除重新焊接。对于重要的焊接接头,还可进行无损检测(如超声波检测、压力测试等),以确保
焊接质量满足要求。
(三)热熔焊接质量控制要点
1. 焊接参数控制
严格控制热熔机的加热温度、加热时间和焊接压力等参数,这是保证焊接质量的关键。不同的塑料材质和管材规格,其***焊接参数有所不同,施工前应根据产品说明书和实际试验确定合适的参数,并在施工过程中严格按照
参数执行。同时,要定期对热熔机的温度进行校准,确保温度显示准确无误。
2. 操作人员技能培训
热熔焊接操作人员的技术水平和经验对焊接质量影响很***。因此,操作人员必须经过专业培训,熟悉热熔焊接的原理、工艺流程和操作要点,掌握热熔机的操作方法和注意事项。在实际操作中,要严格按照规范要求进行操作
,避免因人为因素导致焊接缺陷。
3. 环境条件控制
热熔焊接环境的温度、湿度和风速等因素也会对焊接质量产生影响。一般来说,环境温度应在 5℃以上,湿度不宜过***,风速不宜超过 8 米/秒。在低温、高湿或***风天气条件下进行焊接时,应采取相应的防护措施,如搭设
防风棚、预热管材等,以保证焊接质量。
综上所述,厌氧三相分离器的铺设空间***小需综合考虑多方面因素,通过科学合理的计算和经验参考来确定;而热熔焊接工艺则是保障分离器制作安装质量的重要环节,严格遵循工艺流程和质量控制要点,才能确保三相分离
器的正常运行和长期稳定使用,为工业生产和环境保护提供有力支持。